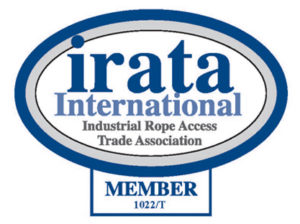
If you’re not familiar with IRATA’s Work &Safety Analysis, then you should be. You can find a copy here. Go ahead, download it and take a look. I’ll wait. This report is a product of IRATA’s requirement that Member Companies report incidents. As important as reporting is, we’ve got to do something with the information. This is where IRATA really shines. I look forward every year to its release. You should, too, if you’re a supervisor or a manager of rope access teams. The report contains so much great information.
Employment
According to the report, the number of employed managers, technicians, and support staff has grown by a bit over 25% from 2022 – 2023, Level 1’s experiencing almost 27% growth, Level 2’s at 17%, and Level 3’s at 18%. Support staff experienced the largest growth in 2023 with a whopping 70%.
Employment by Grade
Level 1
10,629
Level 2
4,503
Level 3
7,964
Managers
1,134
Other
3,439
Total
27,669
Interestingly, the utilization rate for all grades is lower than full time when you consider the number of hours worked per grade, especially among the technicians, about 54%. Utilization simply means of the 2080 work hours available for a technician to work at a full-time job, how many did each technician use? In terms of 2023, each reported technician worked an average of 1,080 hours.
Training is an important part of a growing industry. The industry is spending about 4% of its hours conducting IRATA training. It’s important to keep in mind that these figures are derived from IRATA statistics reported by IRATA Member Companies and do not include the activities of other certifying bodies or non-member companies.
Reporting
Reporting is where IRATA really shines. I completely support the idea of collecting industry statistics. The challenge is to take the data from around the world and distill it into data that is accurate and correct. Different countries have various legislative requirements for reporting accident data. With that in mind, IRATA uses a bit of math to standardize the report. That’s about all I’ll say about the conversion process. Now, let’s get busy with the facts.
As rigorous as IRATA is about its requirement to report incidents and accidents, they continue to struggle. In 2023, IRATA Member Companies reported 356 accidents and incidents. That number is staggeringly low. On average, IRATA receives a reported accident or injury from each of its members once in every two years! To make matters worse, IRATA considers many of the incidents reported from Training Member Companies to be useful, but not relevant to the analysis, more like errors rather than incidents. So, they removed 89 reported incidents from the analysis, making the analysis pool a total of 267, 159 of which occurred “on-rope”.
Now, we are all familiar with the safety triangle or incident pyramid. The base is formed through near-miss reporting, and each successive layer is a smaller number than the previous. The data provided illustrates this idea. I thought it particularly interesting that 7 Member Companies accounted for less than 5% of all hours worked yet represented nearly half of all incidents reported.
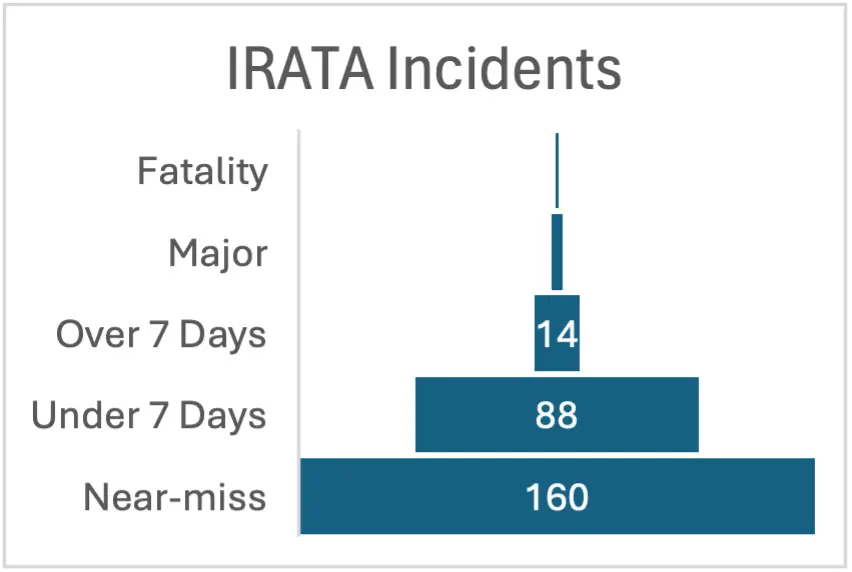
Huh? Does this mean the other 672 Member Companies are doing everything correctly, or does it mean they are neglecting their responsibilities? I get it, there are contributing factors working here, is there a reluctance to air dirty laundry? It could be strictly a cultural difference. My guess is that the answer to that question lies somewhere in between. After all, we are talking about the world-wide rope access population.
One other thing before we move on to more urgent matters – I need to throw a shout out to the Member Companies who make up the North America Regional Advisory Committee. 53 Member Companies contributed to nearly 54% of all of the accident and incident reports.
We must learn from the past if we are to improve the future
Accidents and Incidents
I think this is an appropriate thing to say, especially regarding safety. This graph from the WASA report tells us that we are not improving as well as we should. Our “Over 7 Day” injuries have increased Year over Year (YoY) and the Major injuries have met or exceeded past performance. Unfortunately, our industry suffered a fatality in 2023 as well.
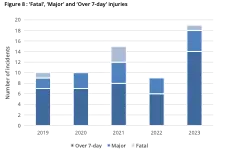
That makes 5 reported fatalities in a 6-year period. IRATA also states there was an additional fatality reported in 2023 but subsequently omitted because it was deemed to have been the result of natural causes. Remember, these numbers do not include activities by companies where the IRATA Member Company reporting requirements do not apply.
Who are involved in these incidents, anyways? Well, the data shows for these three categories, Fatality, Major, and Over 7 Days, that our Level 3 technicians are leading the way. That’s a fact that’s hard to understand. The folks who are supposed to lead the safety efforts at our worksites are the people who are most in harm’s way.
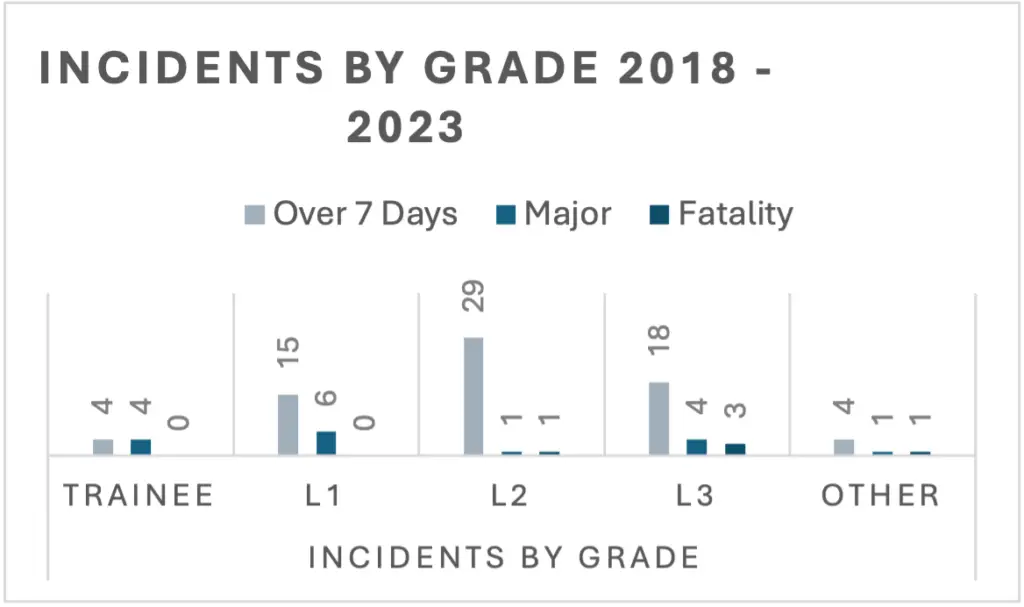
To be clear, it is my understanding that the Fatality listed in the “Other” category was actually a Level 3 who was not “on rope”. On a sidebar, IRATA has changed the format and reporting methods over the years which makes compiling the information quite difficult. Anyways, a lot has changed in our industry over the years, but we have more work to do if we are to improve.
I think it’s also important to take a quick look at what part of the body is most exposed to injury. Historically, most injuries have occurred to a technician’s hands, arms, legs and eyes. 2023 was not much different, other than the legs jumped up to a tie for first, sharing the lead with the hand.
Understanding the immediate cause of any incident is part of our learning process. We need this information so that we can begin to understand the gaps in our safety systems. For instance, IRATA has provided its membership with useful information to further educate candidates about protection of ropes and dropped objects. These learning aids are effective in helping each candidate take personal responsibility for their actions and decisions while at work.

According to the Member Companies’ reports for 2023, these are the top three culprits causing injury to IRATA technicians:
- Operator error or omission.
- Falling or dropped objects
- Contact with tool(s), material or equipment
If you’ve read this far, then I think I’ve got you hooked. There is a great deal more information in the WASA report that you’ll find useful. I’ll leave you with some thoughts, all of which are my own, please leave me yours either in the comments, or you can send them to my email, dhwitter@access-rules.com.
First and foremost, our team at AccessRULES continue to keep the families and friends of our fallen technicians in our thoughts and prayers. It is hard to describe the hardship of losing one you care about, and we hope they can find a way to ease the loss.
Our industry has a responsibility to learn from the accidents and injuries which affect our teams. That’s why reporting these should never be seen as exposure to a company’s bottom line or reputation, but rather an opportunity to prevent pain, suffering and even death. We should find a way to reward the 5% who contribute 50% of the results. Look into the culture of these companies and discover ways to encourage the remaining companies to change their outlook as well. That’s a big task but it can be done. My experiences lead me to believe this. It was only a few decades ago when I felt intimidated by an unsafe culture.
Although culture change is slow and affected by regional influences, a few changes may help immediately. IRATA is the industry leader in rope access guidance and accident and injury reporting. I believe the following small improvements could make a big change.
- Recognize and reward the companies who meet expectations. Make it competitive, give a prize at the annual ITEC.
- Improve the reporting system so that near misses can be easily reported. Include it on the Technician portal. I know, there may be some people who use it for malicious intent. I’m sure there are ways to limit this. Heck, make an app that technicians can use.
- Lobby other certification bodies to begin a form of data collection. If enough members want it, it will happen.
- Encourage your employees to report what happens on the worksite. Again, make it a contest.
- Focus on the behavior of the technician. Management and support staff must talk the talk and walk the walk before the teams will follow.
- Make sure a technician is promoted to a Level 3 role only after they have displayed safe behavior consistently and has the skills to lead a team. This should be done during their tenure as a level 2 technician. The certification process cannot do this – it must be done by the employer.
These and many other projects can make our profession safer to work in. We have thousands of technicians working hard every day on rope access worksites around the world. They deserve more information that can keep them safe at work. Share this with them. Shouldn’t we create a culture to help keep them safe until they return home?
Thanks for tuning in. Until next time – be safe!